1. Une forte irradiation ne garantit pas une production élevée
L’intensité de l’ensoleillement et la température des modules sont les deux facteurs clés qui influencent la puissance de sortie d’un système photovoltaïque.
Bien que l’été offre des journées plus longues et un ensoleillement plus intense, la hausse de la température ambiante entraîne une augmentation significative de la température des panneaux, ce qui réduit leur efficacité de production.
Sous forte irradiation estivale, la température de surface des panneaux installés en toiture peut atteindre 65–75 °C, bien au-delà des conditions standards de test (25 °C). La grande majorité des modules en silicium subit une perte de puissance d’environ 0,3% à 0,35% par degré supplémentaire.
Ainsi, même si l’été présente d’excellentes ressources solaires, la montée en température des modules entraîne une baisse de performance qui impacte directement la production globale. À titre d’exemple, dans les régions chaudes, la puissance instantanée par kilowatt en milieu de journée estivale est souvent inférieure à celle mesurée au printemps ou à l’automne pour un niveau d’irradiation équivalent. Cela explique pourquoi un ensoleillement élevé ne signifie pas forcément une production plus élevée.
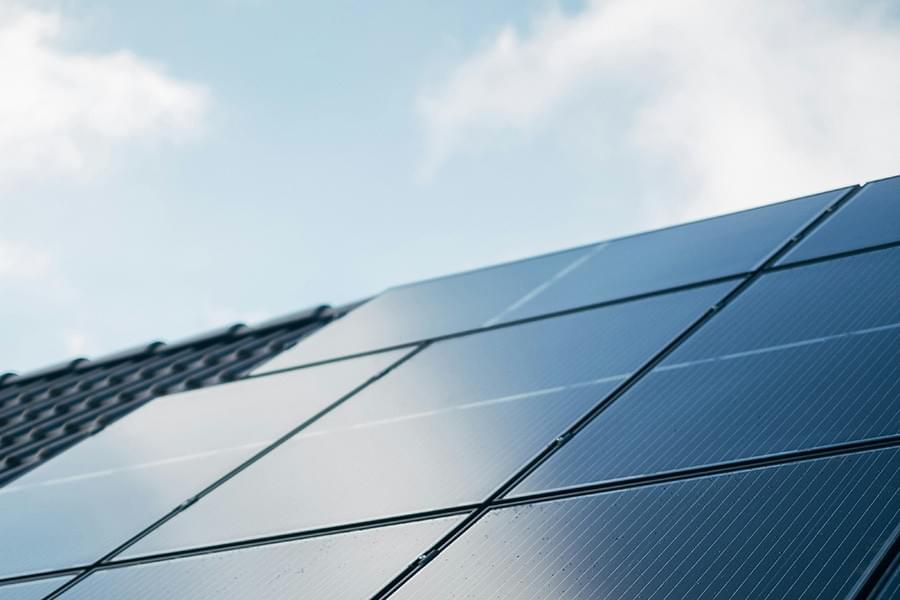
2. Le coefficient de température détermine l’écart de production
La baisse de performance des panneaux photovoltaïques en conditions de chaleur est principalement liée à leur sensibilité électrique à la température. Elle est généralement mesurée par le coefficient de température de la puissance (%/°C), qui indique le pourcentage de perte de puissance maximale par degré supplémentaire.
Plus ce coefficient est faible, meilleure est la résistance thermique du module et plus il conserve de puissance en conditions de forte chaleur.
Dans les conditions d’irradiation élevée de l’été en Europe du Sud, la température de surface des panneaux dépasse fréquemment 65–70 °C, soit un écart de 35 à 45 °C par rapport aux conditions standard de test (25 °C).
Prenons un exemple avec une élévation de température de 40 °C :
- Pour le PERC : –0,34 × 40 = –13,6%
- Pour le HJT : –0,24 × 40 = –9,6%
À température de fonctionnement égale, la différence de puissance instantanée entre les deux atteint environ 4%.
Selon les simulations de PVsyst et les données mesurées en Europe du Sud, l’écart de production annuelle entre les panneaux HJT et PERC dans les régions chaudes se situe généralement entre 3% et 6%. En prenant comme référence une production moyenne de 1 500 kWh/kWp/an, cela représente un gain annuel cumulé de 45 à 90 kWh/kWp, avec un impact direct sur la structure des coûts LCOE et sur les modèles de prévisions financières des projets.
Le coefficient de température influe également sur la conception électrique et le dimensionnement des onduleurs. Pour des projets en autoconsommation ou visant un rendement stable, négliger la dégradation des performances due à la surchauffe peut conduire à une sous-estimation de la capacité réelle de production, affectant ainsi la prévision des rendements et la cohérence des solutions techniques.
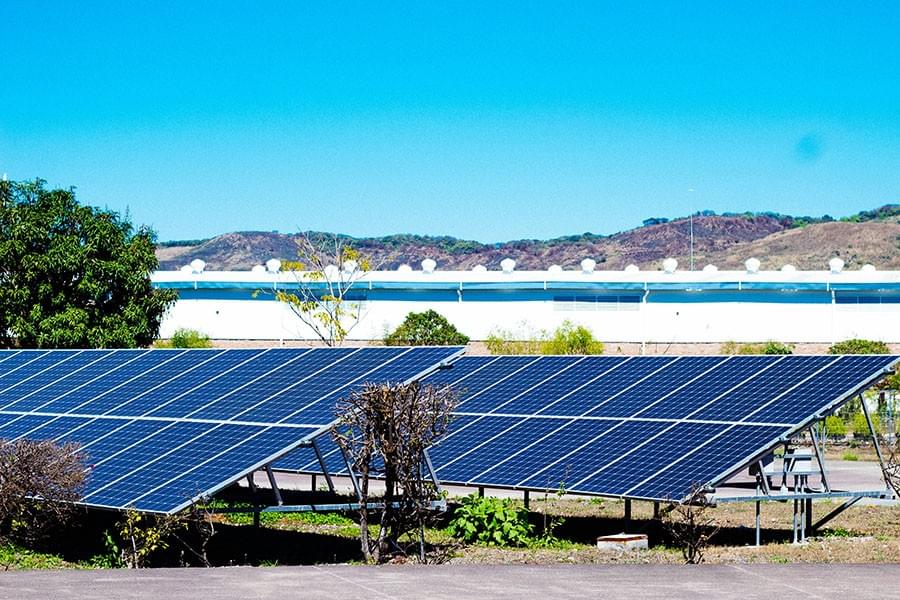
3. Le design structurel influence la résistance thermique
La conception structurelle des panneaux photovoltaïques a un impact direct sur leur stabilité thermique et leur efficacité de fonctionnement en environnement chaud. Les matériaux d’encapsulation, les chemins conducteurs et l’homogénéité du champ thermique sont les principaux facteurs qui déterminent la capacité des modules à résister à la chaleur, en particulier sous forte charge et forte irradiation en été, où ces différences deviennent significativement amplifiées.
Le matériau d’encapsulation est un facteur clé qui influence la dissipation thermique.
Les panneaux à simple verre, grâce à une technologie mature, un poids réduit et un bon rapport qualité-prix, sont encore largement utilisés en Europe centrale et dans les zones tempérées, avec des performances stables. Cependant, le backsheet polymère couramment utilisé (comme le TPT ou le PPE) présente une conductivité thermique limitée, de seulement 0,2 à 0,3 W/m·K, ce qui restreint la dissipation de chaleur en conditions de haute température.
En comparaison, les panneaux double verre utilisent du verre trempé également à l’arrière, avec une conductivité thermique plus élevée de 1,0 à 1,4 W/m·K, permettant de transférer et de dissiper la chaleur de manière beaucoup plus efficace. Les mesures sur le terrain montrent qu’en conditions de forte irradiation et de faible circulation d’air, la température de fonctionnement des panneaux double verre peut être inférieure de 2 à 3°C. Pour un module avec un coefficient thermique de –0,3%/°C, cela équivaut à un gain supplémentaire de puissance de 0,6% à 0,9%, un avantage particulièrement significatif dans le sud de l’Europe et sur les côtes méditerranéennes.
La différence dans la structure conductrice impacte également l’uniformité de la répartition thermique.
Les panneaux conventionnels avec cadre en aluminium utilisent des busbars à l’avant pour la conduction électrique. En cas d’ombrage partiel, de microfissures ou de défauts de soudure, des points chauds peuvent se former dans les zones où les busbars sont plus denses, entraînant une élévation locale de la température.
En revanche, les panneaux avec conduction arrière, contacts à l’arrière ou grilles fines présentent une différence de température de surface (ΔT) beaucoup plus faible, ce qui aide à limiter la concentration de chaleur et les fluctuations de rendement. Les mesures montrent que les panneaux avec optimisation thermique peuvent avoir un ΔT réduit de 1,5 à 2°C, garantissant une plus grande stabilité sous haute température.
La conception structurelle joue également un rôle clé dans la gestion des contraintes mécaniques, l’adaptation à la dilatation thermique et la résistance au vieillissement des matériaux.
Les tests de vieillissement accéléré (85°C / 85% HR pendant 2000 heures) montrent que les panneaux double verre présentent généralement un taux de dégradation inférieur à 2%, tandis que certains panneaux simple verre peuvent atteindre 3 à 4%. Toutefois, la structure double verre, du fait de son poids plus élevé, impose des exigences plus strictes en termes de capacité de charge des toitures et de méthodes d’installation. Pour les projets sur toits légers, il est essentiel de trouver un équilibre entre l’adéquation structurelle et les gains de performance.
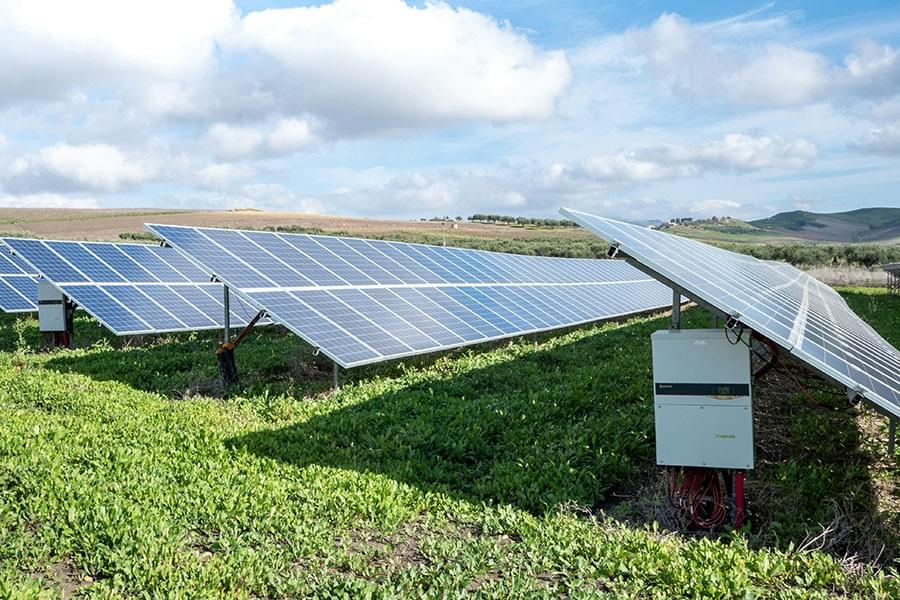
4. Les hautes températures amplifient les différences technologiques
Sous les conditions standard (STC), les différences entre les technologies de modules photovoltaïques sont peu perceptibles. Cependant, en environnement de chaleur constante, ces écarts s’accumulent progressivement et se traduisent par des écarts quantifiables sur la production du système et les modèles de rentabilité.
Avec une température de fonctionnement de 65°C, la différence de coefficient thermique entre les modules PERC et HJT (0,10%/°C) entraîne un écart de production journalière d’environ 3 à 4%. Si la période de haute température représente un tiers du temps de fonctionnement annuel, la différence de production annualisée peut atteindre 2 à 3%, impactant directement le calcul du LCOE et les modèles de prévision de rentabilité.
Sous des conditions combinées de chaleur et de forte irradiation, la structure des modules influence significativement l’efficacité de la dissipation thermique et la vitesse de vieillissement. Les panneaux double verre, grâce à leur conductivité thermique plus élevée et à une encapsulation symétrique, présentent un avantage en termes de stabilité thermique.
Les tests de vieillissement accéléré (85°C / 85% HR) montrent que leur taux de dégradation reste généralement inférieur à 2%, tandis que certains panneaux simple verre peuvent atteindre 3 à 4%. Cependant, les écarts réels dépendent des procédés de fabrication et des matériaux utilisés. Le choix des modules doit donc prendre en compte la température ambiante, les contraintes de charge et la durée de vie prévue du projet.
Les températures élevées accélèrent la formation des hotspots, la propagation des microfissures et la fatigue thermique des zones de soudure. Si le design structurel ne prend pas suffisamment en compte la répartition thermique et la gestion des contraintes, les bords de l’encapsulation deviennent des zones d’accumulation de stress thermique, réduisant la stabilité structurelle du module et augmentant la fréquence des interventions de maintenance.
Dans les marchés dominés par un climat chaud, comme le sud de l’Europe, la gestion de l’élévation de température doit être considérée comme une variable clé pour évaluer l’adéquation technologique. La capacité du module à maintenir sa puissance sous haute température, l’homogénéité du champ thermique et la résistance thermique des matériaux d’encapsulation doivent être des critères essentiels lors de la phase de conception.
Depuis 2008, Maysun Solar produit des modules photovoltaïques de haute qualité, intégrant les technologies avancées IBC, HJT et TOPCon et des stations solaires pour balcons, garantissant performance et fiabilité. Présente à l’international avec des bureaux, entrepôts et des partenariats solides avec les meilleurs installateurs, l’entreprise assure un service optimal. Pour toute demande de devis ou d’informations sur le photovoltaïque, contactez-nous – nos produits vous offrent une qualité garantie.
Références
Fraunhofer ISE. (2024). Photovoltaics Report. Fraunhofer Institute for Solar Energy Systems ISE. https://www.ise.fraunhofer.de/en/publications/studies/photovoltaics-report.html
NREL. (2020). Temperature Coefficients for PV Modules. National Renewable Energy Laboratory. https://www.nrel.gov/docs/fy20osti/76876.pdf
PVsyst SA. (2023). PVsyst Software Documentation – Thermal Behavior of PV Modules. https://www.pvsyst.com/help/thermal_behavior.htm
Lectures recommandées :